The research interest of our group is quite broad. In all of our projects the fundamental understanding of various light-matter and electron-matter interactions are going hand in hand with our application-oriented approach. Our projects are centered around three main topics:
Fabrication, investigation and application of nanostructures
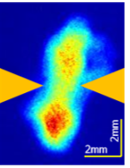
We employ temporally and spatially resolved optical emission spectroscopy suplemented with plasma diagnostic evaluation methods to obtain information on the spark plasma typical for nanoparticle generators. In addition to the general characterization of spark plasmas (such as temperature and electron concentration) we focus on plasma properties that are relevant from the point of view of particle formation.
More information in the following publications: Kohut et al. 2017a, Kohut et al. 2017b
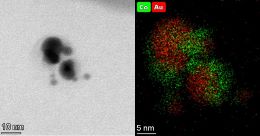
We produce nanoparticles in the gas phase from various materials (Au, Ag, Cu, Pb, Pt, Pd, Co, Ni, Zn, W, etc.) and investigate the particle formation mechanism as well as the properties of the generated nanoparticles. Recently, our interest is mainly focused on the generation and investigation of multicomponent particles with a particular emphasis on tuning their composition.
For more information on the topic please see: Kohut et al. 2021
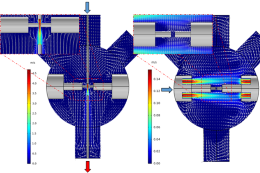
We employ computer fluid dynamics (CFD) simulations to better understand the gas flow field forms in spark discharge nanoparticle generators under different conditions. We also aim at modelling the particle trajectories during their transportation within the generator. More information: Megyeri et al. 2021
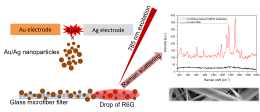
Generating single- and multicomponent nanoparticles with plasmonic properties for different applications is one of our main research directions. In this project we aim at employing spark-based particles to fabricate versatile and efficient platforms for different nanoparticle-enhanced spectroscopies, such as surface-enhanced Raman spectroscopy (SERS) and nanoparticle-enhanced laser-induced breakdown spectroscopy (NE-LIBS).
Further information on our recent results: Kohut et al. 2020, Kohut et al. 2021, Palásti et al. 2022.
Laser materials processing
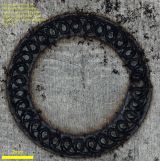
We have a strong application-oriented research focus on laser joining (welding and soldering) and cutting of metallic materials. Recently, we have been working on various aspects of laser joining for optimizing the battery packs of electric vehicles.
For more information please see: Horváth et al. 2020, Körmöczi et al. 2020
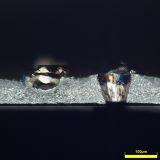
We have solid background in pulsed laser deposition (PLD) for generating homogenous or nanostructured layers of several challenging materials (TiON, ITO, CNx, etc.), spanning the few nm to sub-micrometer thickness range. Patterning (scribing, drilling) materials and especially layer stacks at the micro- and sub-micro levels is also a competence we have.
More information: Szörényi and Geretovszky, 2005, Búzás and Geretovszky, 2012
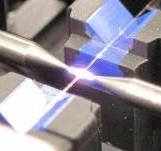
Working on different aspects of laser materials processing with different partners from industry to academia allowed us to acquire skills and expertise in the field of fiber laser development and testing. Specifically, we are involved in projects related to fusion splicing different fiber-optic components often for multi-kW applications. We also investigated non-linear processes, such as Raman scattering in high-power fiber-based laser systems.
Additive manufacturing (3D printing)
Additive manufacturing, or 3D printing as it was called in the last decade, is our newest focus research area. We perform these projects using the unique infrastructure of the 3D Center of University of Szeged.
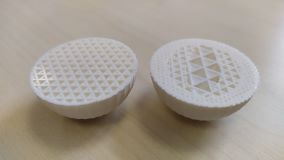
Nowadays, ‘architectured materials’ or briefly archimats have been steadily making their way into mainstream materials science and engineering. This is based on the recognition that tailoring new materials properties and functionalities no longer relies only on traditional approaches (i.e. manipulating a material’s composition and microstructure), but is also possible via changing the inner architecture of the material at a length scale intermediate between the microstructural scale and the specimen dimensions. We investigate this new ‘degree of freedom’ of materials science via designing and measuring archimats after making them with 3D printing.

Tailoring the geometry/shape of an object to its functionality is not a new idea. However, making it possible has two prerequisites: efficient computational power and a manufacturing technology which is capable to turn a digital design into a real object. With cloud computing and the advent/boom of 3D printing today generative design is a vividly studied new field. We investigate the peculiarities of this new alternative to traditional design, and practice and develop new methodologies in order to integrate its principles efficiently with additive manufacturing.
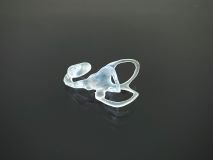
We use additive manufacturing for addressing application-oriented challenges of the health sector. Patient specific implants/surgical guides, printing realistic models for both patient education and supporting the education of medical students and professionals, alike are just two examples from those we serve by additive manufacturing. Pushing the present boundaries of AM technologies is among our ultimate goals for serving the needs of medical treatments, as well as translational research the best we could.
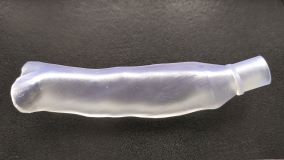
Our goal is to develop a computer model that is suitable for estimating the flow characteristics of segmented tracheas from CT images. We create a computer model of healthy and pathological segmented tracheas, and then simulate their flow conditions. The segmented trachea models will be 3D printed and the mechanical properties will be determined. We create 3D printed trachea models with mechanical properties similar to those of human trachea. We validate the in silico calculations with the help of these models.